Honeycomb substrates are widely used in various industrial applications, including automotive, aerospace, and chemical industries. They are made from various materials such as ceramics, metals, and polymers, and are known for their unique structural properties that make them an ideal material for numerous industrial applications.
In this blog post, we will explore the key features and uses of honeycomb substrates.
What is a Honeycomb Substrate?
A honeycomb substrate is a type of structured material that has a honeycomb-like structure. It is characterized by a series of hexagonal cells that are interconnected to form a continuous network. This structure creates a large surface area that is essential for many applications such as catalysis, filtration, and heat transfer.
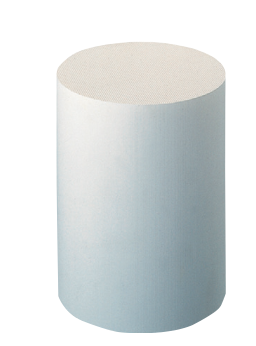
Materials Used for Honeycomb Substrates
Honeycomb substrates can be made from a variety of materials, including ceramics, metals, and polymers. Ceramic honeycomb substrates are widely used in catalytic converters for automobiles, while metallic honeycomb substrates are used for heat exchangers and air filters. Polymer honeycomb substrates are used in various medical applications such as blood oxygenators and artificial lungs.
Properties of Honeycomb Substrates
The properties of honeycomb substrates depend on the materials used in their production. However, some common properties include:
- High Surface Area: The unique honeycomb structure creates a large surface area that is essential for many applications such as catalysis and filtration.
- High Strength: The honeycomb structure provides a high strength-to-weight ratio, making it ideal for aerospace applications.
- Thermal Stability: Honeycomb substrates can withstand high temperatures, making them suitable for use in high-temperature applications such as heat exchangers.
- Chemical Stability: Honeycomb substrates are chemically stable, making them resistant to corrosion and chemical attack.
Uses of Honeycomb Substrates
Honeycomb substrates have numerous industrial applications. Here are some examples:
- Catalytic Converters: Ceramic honeycomb substrates are used in catalytic converters for automobiles. The high surface area of the honeycomb structure allows for the efficient conversion of harmful exhaust gases into less harmful substances.
- Heat Exchangers: Metallic honeycomb substrates are used in heat exchangers to transfer heat between fluids. The high surface area and thermal stability of the honeycomb structure make it an ideal material for this application.
- Air Filters: Metallic and polymer honeycomb substrates are used in air filters to remove pollutants from the air. The large surface area and high strength of the honeycomb structure allow for efficient filtration.
- Medical Applications: Polymer honeycomb substrates are used in various medical applications such as blood oxygenators and artificial lungs. The large surface area and chemical stability of the honeycomb structure make it an ideal material for these applications.
Conclusion
In conclusion, honeycomb substrates are a versatile material with unique structural properties that make them ideal for numerous industrial applications. They can be made from a variety of materials and offer high surface area, strength, thermal stability, and chemical stability. Honeycomb substrates are used in catalytic converters, heat exchangers, air filters, and medical applications.
Structure and Manufacturing
The honeycomb structure of the substrate is created by stacking sheets of material and then corrugating them into a hexagonal shape. The sheets are then bonded together to form a continuous network of cells.
The manufacturing process for honeycomb substrates can vary depending on the material being used. For example, ceramic honeycomb substrates are typically made using extrusion, while metallic honeycomb substrates are made using roll bonding. Polymer honeycomb substrates can be made using various techniques such as extrusion or injection molding.
Applications
Honeycomb substrates are used in a wide range of industrial applications, as we’ve mentioned before. Here are some additional examples:
- Water Treatment: Honeycomb substrates can be used as a filter media for water treatment. The large surface area and high porosity of the honeycomb structure allow for efficient removal of contaminants.
- Sound Absorption: Honeycomb substrates can be used for sound absorption in architectural applications. The unique structure of the honeycomb allows for the absorption of sound waves, reducing noise levels.
- Energy Storage: Honeycomb substrates can be used as a substrate for energy storage materials, such as batteries and supercapacitors. The large surface area and high porosity of the honeycomb structure can enhance the performance of these materials.
- Building Materials: Honeycomb substrates can be used in the construction of building materials such as lightweight panels and walls. The high strength-to-weight ratio of the honeycomb structure can reduce the overall weight of the building while maintaining strength.
Conclusion
Honeycomb substrates are a unique and versatile material with a wide range of applications. They offer high surface area, strength, thermal stability, and chemical stability, making them ideal for numerous industrial applications. The manufacturing process for honeycomb substrates varies depending on the material being used, and they can be used for water treatment, sound absorption, energy storage, and building materials, among other applications.
Advantages of Honeycomb Substrates:
- High Surface Area: Honeycomb substrates have a unique structure that creates a large surface area, making them ideal for many applications such as catalysis, filtration, and heat transfer.
- High Strength-to-Weight Ratio: The honeycomb structure provides a high strength-to-weight ratio, making it ideal for use in aerospace and other weight-sensitive applications.
- Thermal Stability: Honeycomb substrates can withstand high temperatures, making them suitable for use in high-temperature applications such as heat exchangers.
- Chemical Stability: Honeycomb substrates are chemically stable, making them resistant to corrosion and chemical attack.
- Customizable: The size and shape of the honeycomb structure can be customized to suit specific applications, allowing for greater design flexibility.
Disadvantages of Honeycomb Substrates:
- Cost: Honeycomb substrates can be expensive to manufacture, particularly those made from ceramics or metals.
- Brittle: Ceramic honeycomb substrates can be brittle and prone to cracking or breaking under stress.
- Limited Applications: Honeycomb substrates are not suitable for all applications, and their use is typically limited to specific industries such as automotive, aerospace, and chemical.
- Manufacturing Complexity: The manufacturing process for honeycomb substrates can be complex and time-consuming, particularly for those made from ceramics or metals.
- Recycling Challenges: The materials used to manufacture honeycomb substrates can be difficult to recycle, particularly those made from ceramics or metals.
Conclusion:
Honeycomb substrates offer a unique combination of properties that make them ideal for many industrial applications. Their high surface area, strength-to-weight ratio, thermal and chemical stability, and customizability make them a versatile material for use in aerospace, automotive, and other industries. However, honeycomb substrates can be expensive to manufacture, and their use is typically limited to specific applications. Additionally, ceramic honeycomb substrates can be brittle and prone to cracking, and the materials used to manufacture them can be difficult to recycle.