The sectioned common rail pump and injector is a key component in modern diesel engines, providing efficient fuel delivery and injection. In this blog, we will explore what a sectioned common rail pump and injector is, how it works, and its benefits in diesel engines.
What is a sectioned common rail pump and injector?
A sectioned common rail pump and injector is a type of fuel injection system that uses a common rail to store pressurized fuel that is then injected into the engine’s combustion chamber. The common rail is a high-pressure fuel delivery system that supplies fuel to the injectors at the precise moment they are needed.
The sectioned common rail pump and injector is comprised of several key components, including the high-pressure fuel pump, common rail, fuel injectors, and fuel pressure regulator. These components work together to provide a reliable and efficient fuel delivery system for modern diesel engines.
How does a sectioned common rail pump and injector work?
The sectioned common rail pump and injector works by storing pressurized fuel in the common rail. The high-pressure fuel pump delivers fuel to the common rail, which then supplies fuel to the fuel injectors. The fuel injectors are controlled by an electronic control unit (ECU) that monitors the engine’s operating conditions and adjusts the fuel delivery accordingly.
When the ECU signals the injectors to deliver fuel, a small amount of fuel is released into the combustion chamber at a high pressure. This atomized fuel then combusts with the air in the chamber, providing the power to move the engine’s pistons.
The fuel pressure regulator ensures that the pressure in the common rail remains consistent, allowing for precise fuel delivery to the injectors. This precise fuel delivery ensures that the engine runs smoothly and efficiently.
What are the benefits of a sectioned common rail pump and injector?
There are several benefits of a sectioned common rail pump and injector in diesel engines, including:
- Improved fuel efficiency: The precise fuel delivery provided by the sectioned common rail pump and injector improves the engine’s fuel efficiency, reducing the amount of fuel consumed per mile driven.
- Reduced emissions: The efficient combustion provided by the sectioned common rail pump and injector results in reduced emissions, helping to meet emissions regulations.
- Improved performance: The precise fuel delivery and combustion provided by the sectioned common rail pump and injector result in improved engine performance, providing more power and torque to the wheels.
- Reduced noise and vibration: The sectioned common rail pump and injector reduces noise and vibration in the engine, providing a smoother and quieter driving experience.
In conclusion, the sectioned common rail pump and injector is a key component in modern diesel engines, providing efficient fuel delivery and injection. The precise fuel delivery provided by the system results in improved fuel efficiency, reduced emissions, improved performance, and reduced noise and vibration. As diesel engines continue to evolve, the sectioned common rail pump and injector will likely play an even greater role in providing reliable and efficient fuel delivery to diesel engines.
One important aspect to understand about the sectioned common rail pump and injector is the high pressure at which fuel is delivered to the combustion chamber. The fuel pressure in the common rail can reach as high as 30,000 PSI (pounds per square inch), which is significantly higher than the fuel pressure in older diesel engines that used conventional fuel injection systems.
This high pressure fuel delivery allows for better atomization of the fuel, which means the fuel is broken down into smaller droplets that can be more easily mixed with air in the combustion chamber. This results in a more efficient and complete combustion of the fuel, which improves fuel economy and reduces emissions.
Another advantage of the sectioned common rail pump and injector is its ability to vary the amount of fuel delivered to each cylinder of the engine independently. This is achieved through the use of solenoid valves in the injectors that are controlled by the engine’s electronic control unit (ECU). The ECU monitors the engine’s operating conditions, such as engine speed, load, and temperature, and adjusts the fuel delivery accordingly to optimize engine performance and fuel economy.
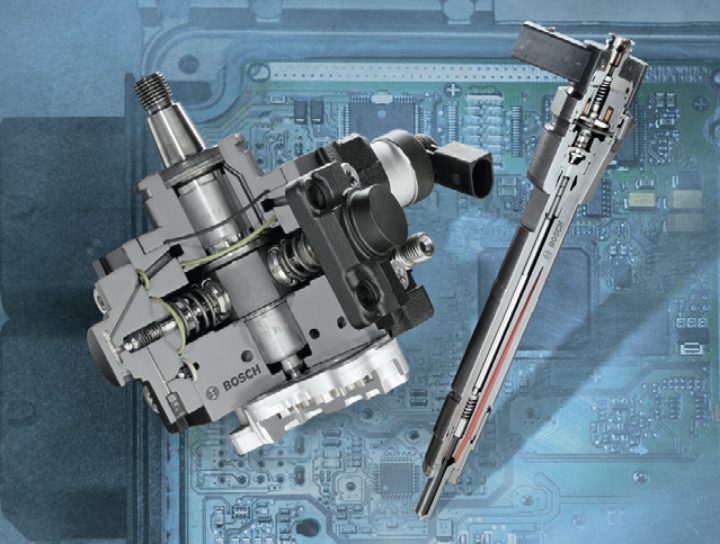
The sectioned common rail pump and injector also allows for more precise control over the timing of fuel delivery, which can have a significant impact on engine performance. By adjusting the timing of fuel delivery, the ECU can optimize the combustion process to achieve the best possible balance between power and fuel economy.
One potential downside of the sectioned common rail pump and injector is its cost. The system is more complex and expensive than older fuel injection systems, which can make it more costly to repair or replace if something goes wrong. However, the benefits of improved fuel economy, reduced emissions, and improved engine performance can often outweigh the initial cost of the system.
Overall, the sectioned common rail pump and injector is a highly advanced fuel injection system that provides significant benefits for modern diesel engines. Its ability to deliver fuel at high pressure, independently control fuel delivery to each cylinder, and precisely time fuel delivery allows for improved fuel economy, reduced emissions, and improved engine performance.
Advantages:
- Improved Fuel Efficiency: One of the biggest advantages of a sectioned common rail pump and injector system is its ability to deliver fuel at high pressure and with precise timing. This results in improved fuel efficiency and can reduce the amount of fuel consumed per mile driven.
- Reduced Emissions: The efficient combustion provided by the system results in reduced emissions, helping to meet emissions regulations. The system can also reduce particulate emissions by atomizing the fuel more effectively.
- Improved Performance: The precise fuel delivery and combustion provided by the sectioned common rail pump and injector system result in improved engine performance. The system can provide more power and torque to the wheels, which can improve acceleration and overall performance.
- Reduced Noise and Vibration: The system can reduce noise and vibration in the engine, providing a smoother and quieter driving experience.
- Flexibility: The system is flexible in terms of fuel type and can be used with a wide range of fuels, including biodiesel and synthetic fuels.
Disadvantages:
- Cost: One of the biggest disadvantages of a sectioned common rail pump and injector system is its cost. The system is more complex and expensive than older fuel injection systems, which can make it more costly to repair or replace if something goes wrong.
- Maintenance: The system requires regular maintenance to ensure that it operates correctly. This can include cleaning the fuel injectors and replacing worn or damaged components.
- Complexity: The system is more complex than older fuel injection systems, which can make it more difficult to diagnose and repair if something goes wrong.
- Durability: Some components of the system, such as the high-pressure fuel pump, can be prone to wear and failure over time. This can result in reduced system performance and increased maintenance costs.
- Risk of Contamination: The high-pressure fuel delivery system used in a sectioned common rail pump and injector system can be more susceptible to contamination from dirt, water, or other debris. This can cause damage to system components and result in reduced performance or failure.
Overall, the advantages of a sectioned common rail pump and injector system outweigh the disadvantages, particularly in terms of improved fuel efficiency, reduced emissions, and improved engine performance. However, the system’s complexity, cost, and maintenance requirements should also be considered when evaluating its suitability for a particular application.