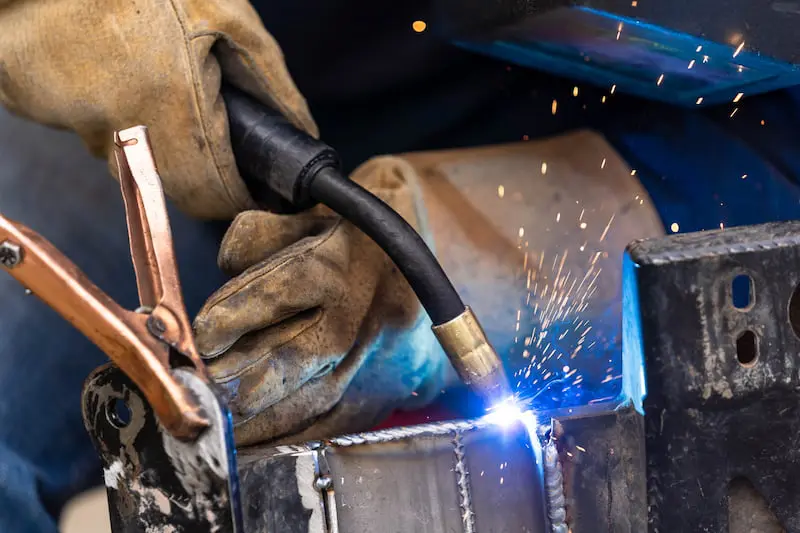
MIG welding has become an increasingly popular method for repairing and restoring car bodies. This process, also known as Gas Metal Arc Welding (GMAW), uses a wire electrode and a shielding gas to fuse metal together. Compared to other welding techniques, MIG welding offers several advantages for car body repairs.
One of the biggest benefits of MIG welding is that it creates a strong, clean, and precise bond between the metal pieces. This is especially important for car bodies, which require a seamless and uniform finish to maintain their structural integrity. MIG welding also produces less heat than other welding techniques, which reduces the risk of warping or distortion in the metal.
Another advantage of MIG welding in car body repairs is that it allows for greater control and flexibility. With MIG welding, the welder can easily adjust the voltage and wire speed to achieve the desired results. This makes it possible to weld different types and thicknesses of metal, which is essential for repairing complex car body structures.
MIG welding also produces less splatter and sparks, which makes it a safer and cleaner option for car body repairs. The shielding gas used in MIG welding helps to protect the weld from atmospheric contaminants, resulting in a stronger and more consistent weld.
Overall, MIG welding is a reliable and effective method for repairing and restoring car bodies. If you’re looking to restore a classic car or repair a damaged vehicle, consider using MIG welding to achieve the best possible results. With the right technique and equipment, you can create a seamless and durable finish that will help your car look and perform its best for years to come.
MIG welding, or Gas Metal Arc Welding (GMAW), is a popular welding technique that uses a wire electrode and a shielding gas to fuse metal together. This method is widely used in various industries, including automotive repair and manufacturing, due to its many advantages. However, like any welding technique, it also has its drawbacks. In this article, we will take a closer look at the advantages and disadvantages of MIG welding.
Advantages of MIG Welding:
- Speed: MIG welding is a fast welding technique that can be used to join thick and thin metals. It uses a continuously fed wire electrode, which makes the welding process much faster than other welding techniques.
- Precision: MIG welding is known for its precision, which is why it is often used in automotive manufacturing. This welding method allows for a high degree of accuracy, which is essential when working with complex car parts and structures.
- Cleanliness: MIG welding produces less spatter and sparks than other welding techniques, which makes it a cleaner option for automotive repair and manufacturing. It also produces a clean and uniform weld that looks better than other welding methods.
- Versatility: MIG welding can be used to weld a wide range of materials, including aluminum, stainless steel, and mild steel. This makes it a versatile welding technique that can be used for various automotive repair and manufacturing applications.
- Easy to Learn: MIG welding is relatively easy to learn and can be mastered quickly. This makes it a popular choice for novice welders who want to learn how to weld car bodies.
Disadvantages of MIG Welding:
- Cost: MIG welding requires a more expensive setup than other welding techniques. The equipment, wire, and shielding gas can be expensive, which can be a disadvantage for small-scale automotive repair and manufacturing businesses.
- Limited penetration: MIG welding has limited penetration, which means it may not be suitable for welding thicker materials. This is a disadvantage if you need to weld thick car parts.
- Gas availability: MIG welding requires a shielding gas to protect the weld from atmospheric contamination. This can be a disadvantage if you don’t have access to the necessary gases, which can limit your welding capabilities.
- Difficult in windy conditions: MIG welding requires a steady hand and a controlled environment. Windy conditions can disrupt the shielding gas and make welding more difficult.
- High heat input: MIG welding produces more heat than other welding techniques, which can increase the risk of warping and distortion in thin metals. This can be a disadvantage when welding car bodies that require a seamless and uniform finish.
In conclusion, MIG welding is a versatile and precise welding technique that is widely used in the automotive industry. Its advantages include speed, precision, cleanliness, versatility, and ease of learning. However, its disadvantages include cost, limited penetration, gas availability, difficulty in windy conditions, and high heat input. Before choosing MIG welding for automotive repair and manufacturing, it is essential to consider these advantages and disadvantages to determine if it is the right choice for your specific needs.